This website uses cookies so that we can provide you with the best user experience possible. Cookie information is stored in your browser and performs functions such as recognising you when you return to our website and helping our team to understand which sections of the website you find most interesting and useful.
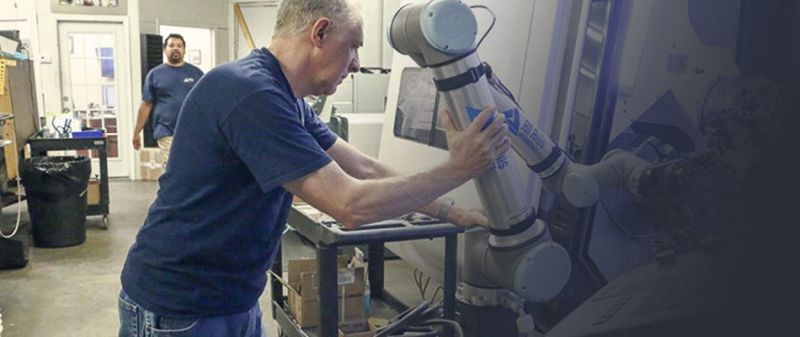
Cobots Handle Glazing and Clay Forming tasks at Finnish Ceramic Factory, Improving Ergonomics and Throughput
01 THE SHORT STORY
Pentik, the northernmost ceramic factory in the world, located in Posio, Finland, wanted to automate its high mix/low volume production without losing its craftsman identity. The company chose two UR10 collaborative robots from Universal Robots to replace the heavy, repetitive tasks of glazing and molding tableware, ensuring a uniform outcome that also improves the ergonomics of Pentik’s employees. The cobots now work in tandem with humans, delivering the same touch of human handicraft as before, while increasing the work efficiency at the workstation tenfold.
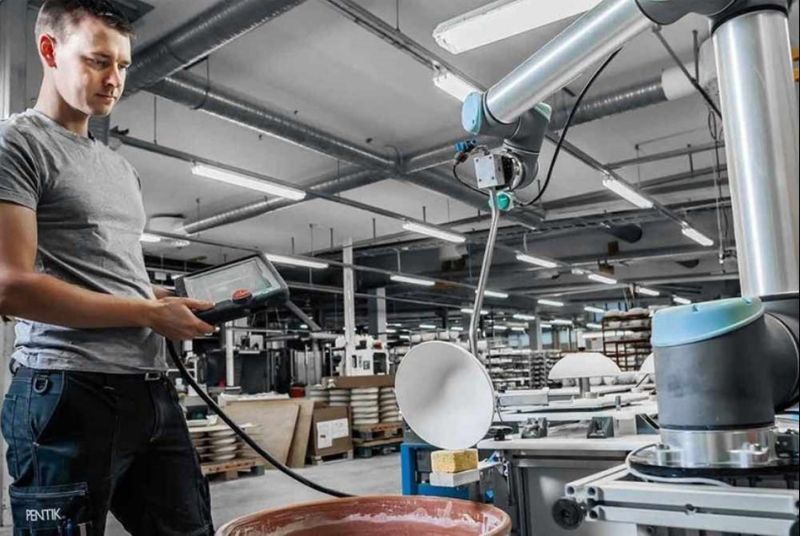
02 THE CHALLENGE
Nearly all ceramic factories in Western countries have moved their mass production to low-cost regions. Ceramic artist Anu Pentik who founded Pentik in 1971 proudly defends craftsmanship. His company wanted to swim against the tide by creating all its ceramic products in Posio, a Finnish municipality located only a few kilometers south of the Arctic Circle.
The making of ceramics is manual labor. When a worker glazes tableware and shape dishes with a tool, they will repeat the same task hundreds of times a day. Tasks that are hard on the hands, shoulders and backs of the workers.
Pentik wanted to find a solution that enabled production automation while utilizing experienced employees’ skills for tasks of higher added value such as quality control. Freeing up workers from having to perform ergonomically unfriendly, monotonous tasks would also improve the employer’s image.
03 THE SOLUTION
Nearly all ceramic factories in Western countries have moved their mass production to low-cost regions. Ceramic artist Anu Pentik who founded Pentik in 1971 proudly defends craftsmanship. His company wanted to swim against the tide by creating all its ceramic products in Posio, a Finnish municipality located only a few kilometers south of the Arctic Circle.
The making of ceramics is manual labor. When a worker glazes tableware and shape dishes with a tool, they will repeat the same task hundreds of times a day. Tasks that are hard on the hands, shoulders and backs of the workers.
Pentik wanted to find a solution that enabled production automation while utilizing experienced employees’ skills for tasks of higher added value such as quality control. Freeing up workers from having to perform ergonomically unfriendly, monotonous tasks would also improve the employer’s image.
The dents are made using two 40 mm wet orbital sanding sponges. In the plate finishing cell, the cobot picks up the tableware from an automatic moulding line, and then – depending on the product – the robot places it up against either a horizontal or vertical sanding sponge used for forming.
According to Lassi Kaivosoja, the greatest challenge was to pinpoint the accurate pressure in order for the cobot to produce the desired form when working with clay. Sanding sponges are springy, so their pressure is not monitored. With a bit of testing the programmer got it adjusted to the needed pressure for Pentik’s creamics production.
The vacuum grippers include a motor with a bevel gearbox and a pneumatic slip ring. These enable the unlimited and programmable rotation of the suction cup.
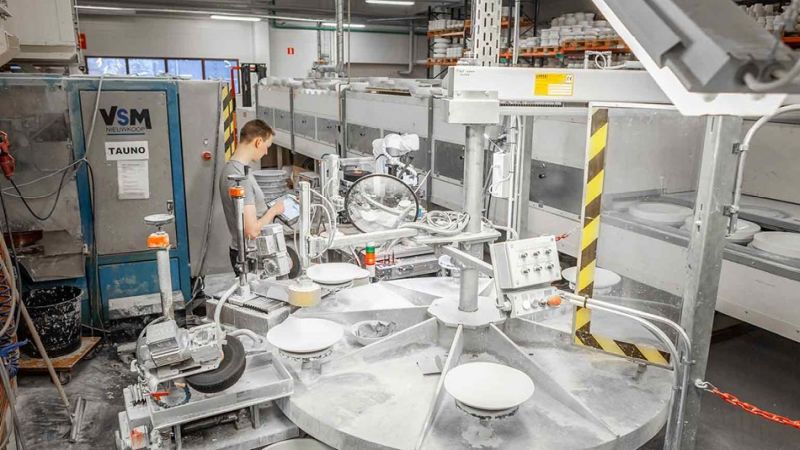
Related Posts
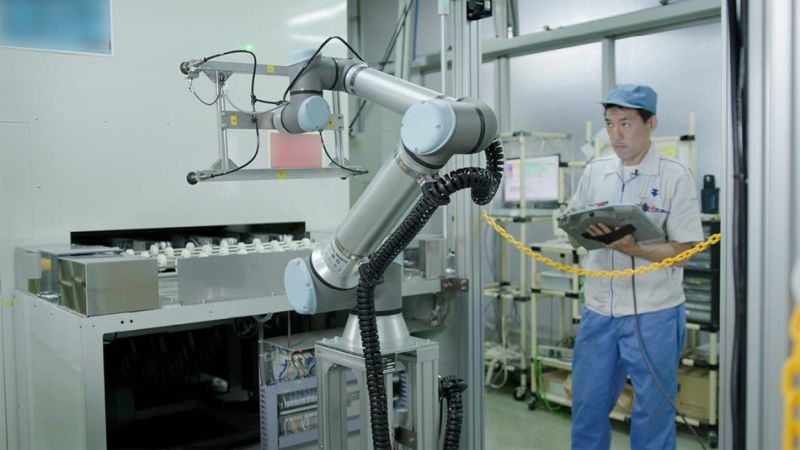
MATSUNAMI GLASS IND., LTD.
UR Cobots Help Matsunami Glass Achieve a 50% Increase in Production 01THE SHORT STORY Matsunami Glass Ind., Ltd. manufactures various types of glass for microscopic, medical, and electronics applications. The company found that using conventional…
- May 25, 2022